Segment Coil Cut Off Saw
MACHINE MANUFACTURING COMPANY IN ALBANY, NY
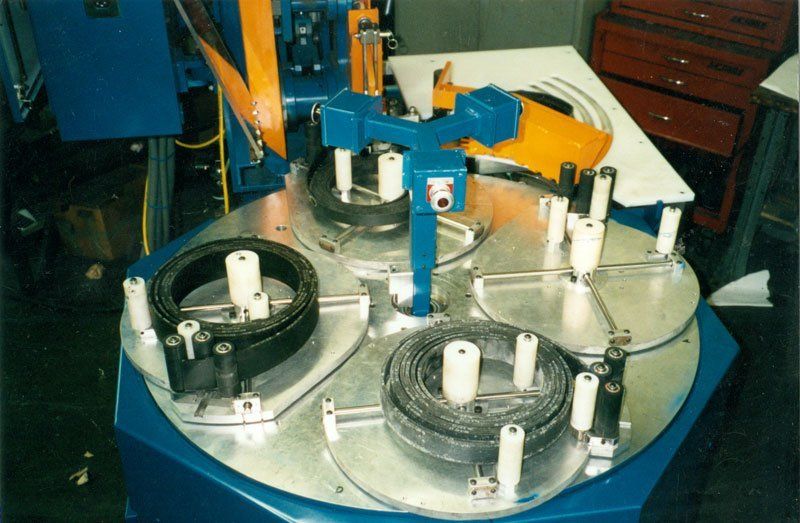
The Segment Saw operation is to cut the spiral roll of molded brake material into the lengths required. The roll of molded material will be manually loaded onto one of the four stations, automatically taken to the cutting station, cut into lengths, and then stacked in the exit area. The cutting length is entered into the keypad on the operator station which controls the rotation of the servo motor and therefore the length of segment cut. The machine can cycle continuously at a rate of 1.25 seconds per segment cut and a 2.5 second roll index/set-up time. Example: A .250 thick x 2.00 high x 30 foot long roll is to be cut into 1 foot long pieces, this requires 37.5 seconds and adding 2.5 seconds for index/set-up, yields 30 pieces every 40 seconds (this is a rate of 45 per minute). Machine is designed to handle rolls with a maximum outside diameter of 16 inches, a thickness from .125 to .375 inches, and a width from 1.00 to 3.75 inches.
The index table carries the four (4) carousals from the operator lining load area to the saw unit. The lining on the carousal will auto thread into the infeed mechanism. The index table is mounted on a Camco indexer driven by an AC variable frequency electric motor. The index table carries the four (4) carousals over a cam track that keeps the carousals retracted over the table until the carousal arrives at the saw station.
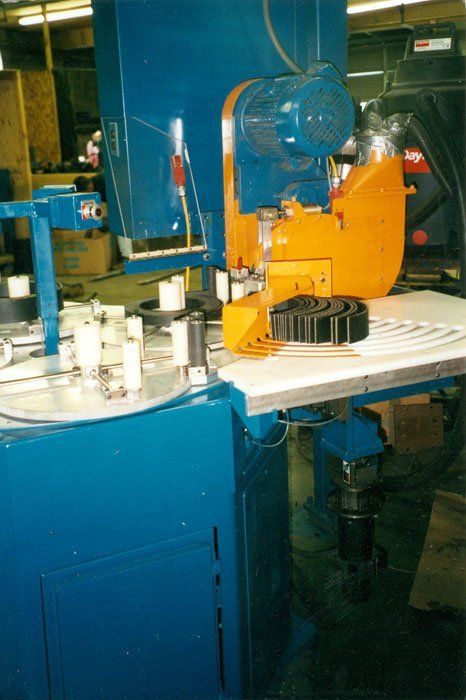
Each carousal has a set of rollers to correctly position the spiral roll and prevent the unwound portion of the roll from rubbing portions of the machine. An additional set of rollers with one direction needle bearings allows the operator to insert the end of the roll of brake material through to the position indicated by the marker. This additional set of rollers allows the auto threading of the lining into the infeed mechanism. The operation of the auto threading is for the drive roll to retract, opening a clear area for the lining. The carousal is carried to the infeed area and is allowed to rotate by the cam track to place the end of the lining between the drive roller and the idler roller. The drive roller clamps the lining material, advances it to the ‘trim end position’, the saw trims the end, and the drive advances the material the desired amount.
The exit mechanism consists of a spring loaded roller to push the cut segment lining out of line with the next segment being cut. This allows the cut segment to stack which will allow easier unloading.
The unload device accepts the number of cut segment linings entered into the keypad, the saw cutting stops, the unload device moves the stack of lining onto the unload table, returns to its original position, and the cutting continues. The unload device will hold approximately 7 inches of lining. The unload device must be at the unload table position for the table to index. The unload device is driven by an air cylinder.